This case study examines the static stress analysis conducted on the underground portion of a Seawater Network in a Gas Field development project. The underground lines were constructed using fiberglass, necessitating a thorough stress evaluation to ensure system integrity and longevity.
Analysis Methodology
Engineers utilized existing mechanical piping models provided by the client as input for the stress calculations. Pipe and fitting thicknesses were implemented according to the received information and in compliance with the ISO 14692 stress code.
The stress analysis was performed using CAESAR II pipe stress software, an industry-standard tool for such evaluations. Pipe stresses were compared to material allowable envelopes constructed based on the guidelines of the ISO 14692 stress code. The system was analyzed for design conditions, including hydrotest scenarios.
To ensure comprehensive analysis, continuations of the analyzed system were included in the model for overlap purposes, providing a more accurate representation of the entire network.
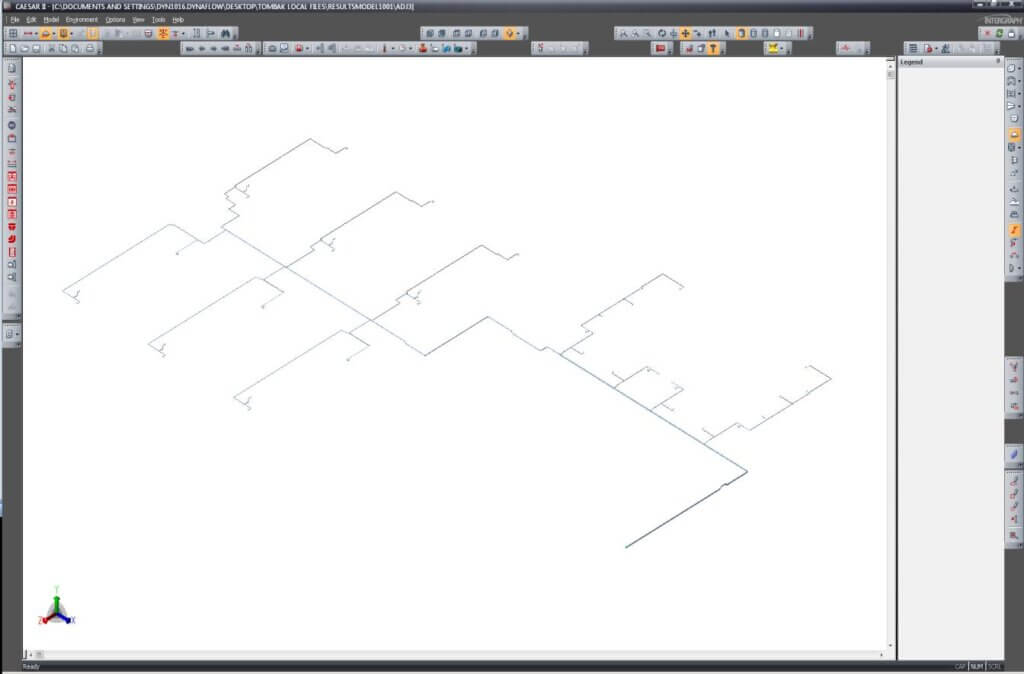
Based on the detailed analysis, engineers proposed several modifications to enhance the system’s performance and durability:
- Reinforcement of piping through additional laminate application.
- Implementation of polystyrene wrapping for added protection.
- Removal of all thrust blocks, likely due to their ineffectiveness or potential to cause stress concentrations.
- Introduction of two drag anchors in the 54″ piping to provide strategic support.
- Installation of three-way stops at above-ground DN50 piping sections.
The analysis also considered the presence of flanges in the system, located at pits and at connections to above-ground steel piping. Engineers anticipated low flange loads at the pits, while higher loads were expected at connections to the above-ground piping.
Key Takeaways
- Static stress analysis is crucial for ensuring the integrity of underground fiberglass seawater networks in gas field developments.
- Compliance with international standards like ISO 14692 is essential for proper stress evaluation and system design.
- Advanced software tools such as CAESAR II enable accurate modeling and analysis of complex piping systems.
- Strategic modifications, including reinforcement, protective wrapping, and anchor placement, can significantly improve system performance.
- Consideration of flange loads at critical connection points is vital for overall system integrity.
This case study highlights the importance of thorough stress analysis in the design and modification of underground fiberglass piping systems. By employing advanced analytical techniques and proposing targeted improvements, engineers can enhance the reliability and longevity of critical infrastructure in gas field developments.