Safety Factors in Fiberglass Engineering
by Mick Bouman (Fiberglass Engineering)
For a pipe system or an individual component an engineer must always verify whether the strength or stability is sufficient for its intended purpose. This verification process requires that the calculated stresses are below the failure stress. Since engineering and manufacturing are not perfect, engineers do not design up to failure but apply safety factors. But what should this safety factor be?
Historically, safety factors used in the piping industry were based on experience. High incidence of failures is a measure of a safety factor that is too low. And so, over the years, safety factors have evolved to what they are today. A different approach to safety factors, rather than trial and error, is making use of the theory of probability. It is possible to determine the chance that the true component stresses are above the true material capacity using the variability of material properties and of geometrical properties of a component. This chance is called the “probability of failure”. By defining an acceptable probability of failure, it becomes possible to determine how far the calculated stresses and the documented material capacity have to be separated to arrive at a sufficiently low probability of failure. This distance between the material capacity and the calculated stress is the safety factor.
This approach has been a part of the Eurocode for some time and is currently also being adopted by new standards that are developed within ISO TC138 SC06. The new standard for FRP design currently being written, with the title “System design of above ground pipe and joint installations without end‐thrust”, also adopts this approach to safety factors. The document is now nearing completion and will soon be issued to ISO after which the member countries of ISO will be able to vote and comment on the document. Mick Bouman is part of ISO TC138 SC06 working group 5 on behalf of Dynaflow Research Group.
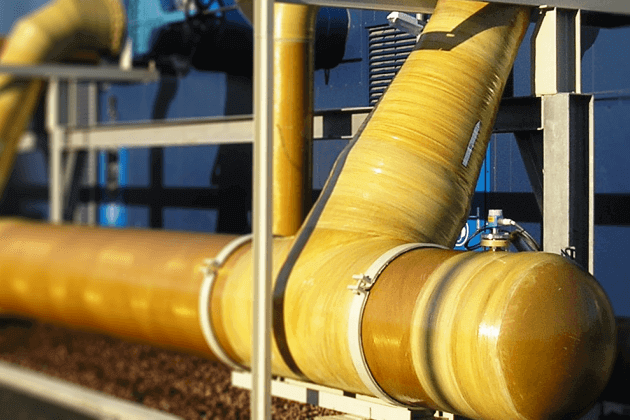