Introduction
A plant in Asia requested a simulation study to be performed, both fluid mechanical (acoustical) and mechanical, of the compressor piping between the first stage discharge and the second stage suction. The second-stage bypass lines were included in the analysis.
Analysis
In the first approach, the acoustical and mechanical natural frequencies were determined to verify the possible occurrence of vibration resonance in the downstream piping.
In a second approach, the mechanical natural frequencies of the system were examined to verify the possible occurrence of vibration resonance in the downstream piping. In the third and last step, an acoustical simulation was performed to verify the pressure oscillations and the unbalanced loads (the shaking forces).
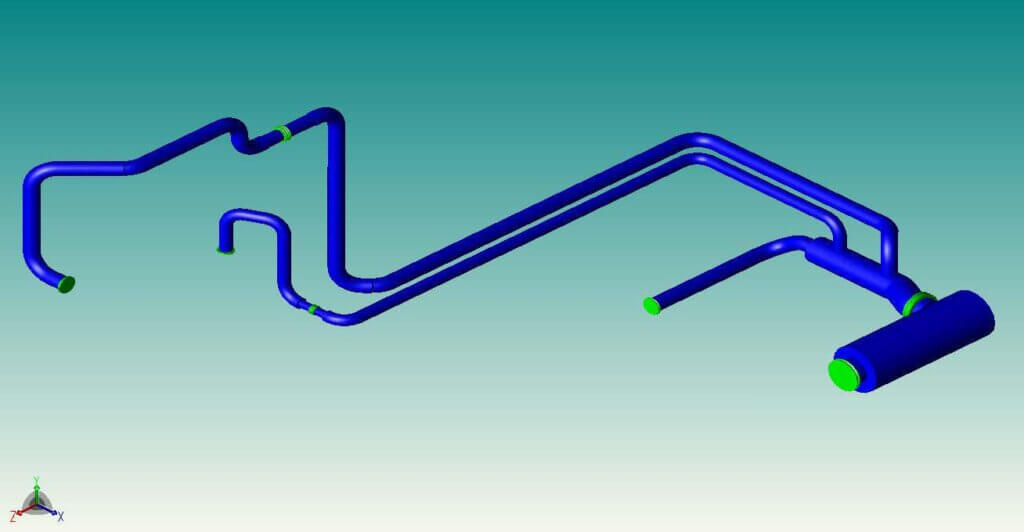
In parallel to the simulation two manual calculations were performed to estimate the pressure oscillations at the compressor first stage discharge nozzle in the absence of the effects of wave reflections. The manual calculation was based on the participation of the nozzle volume in the effect of the compressor plenum.
The manual calculations were repeated for a flow oscillation with an amplitude of 4.59 m3/s, assuming that the flow is completely start-stop.
“Both pressure pulsations and stress levels are acceptable for the discharge piping when the bottle internals are removed.”
Results
The simulation results for the empty bottle condition show pressure pulsation levels in the discharge piping of 0.01 barg level.
The response analysis shows cyclic stress levels with an amplitude of 13 MPa which is well below the endurance limit.
The simulation demonstrates that both pressure pulsations and stress levels are acceptable for the discharge piping when the bottle internals are removed.