Introduction
In the examination of our client’s initiative to assess and enhance the primary cooling water system within an established power plant, various configurations, and operational modes were scrutinized. The primary cooling water flow was found to be adaptable, functioning either as an open loop or as a closed loop system.
In the “closed” loop configuration, the cooling water pumps extracted water from the intake basin under the cooling tower, channeling it through the main condenser units before returning it to the atmospheric cooling tower. Conversely, in the open loop setup, the main cooling water pumps drew water from the Maas River, directing it to the condensers, and subsequently, via a spill, back into the Maas River.
Analysis
A comprehensive analysis was conducted to validate the hydraulic integrity of the system, encompassing fifteen distinct load scenarios. Among these, seven scenarios pertained to pump activations and deactivations. Each of these seven scenarios was meticulously examined under both operational modes, accounting for cooling tower operation and open loop operation i.e. from the Maas River into the Maas River.
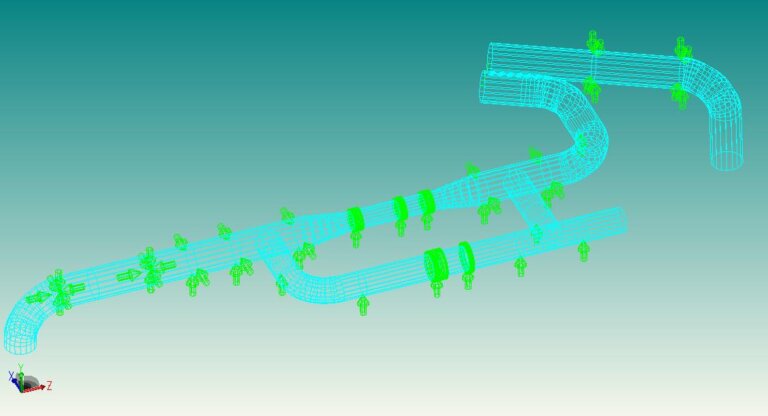
Furthermore, beyond the pump-related cases, an additional scenario was explored concerning the failure of check valve damping. It was assumed that midway through the check valve closure process, the damping mechanism malfunctioned. This particular scenario was scrutinized, with a focus on cooling tower operation, where the system experiences the highest back pressure.
For the pump deactivation scenarios, two distinct conditions were delineated: a single pump trip and the simultaneous tripping of both pumps.
For the pump trip cases, two different conditions have been distinguished:
- One pump trip and
- Both pumps trip simultaneously
Results
Upon completion of the analysis, the results indicated that the ultimate phase of the check valve closure process significantly influenced the maximum pressure buildup when backflow was promptly obstructed. Additionally, the disparities between a 2-step and a 3-step damping system were found to be relatively negligible. To provide a benchmark, several analyses were conducted for an ideal check valve—an instance where the valve closes instantaneously upon reversal of flow direction.