Failure Analysis And Investigation
At Dynaflow, we specialize in solving complex failure problems that arise from dynamic effects due to flow. With over 35 years of experience, our team of experts is dedicated to identifying the root causes of equipment failure and providing effective, long-term solutions.
Our goal is not just to fix the issue but to offer preventive measures that ensure the system’s efficiency, reliability, and longevity. With our extensive experience across a range of industries—from oil and gas to petrochemicals and utilities—Dynaflow is the ideal partner for tackling even the most challenging failure analysis projects caused by flow-related phenomena.
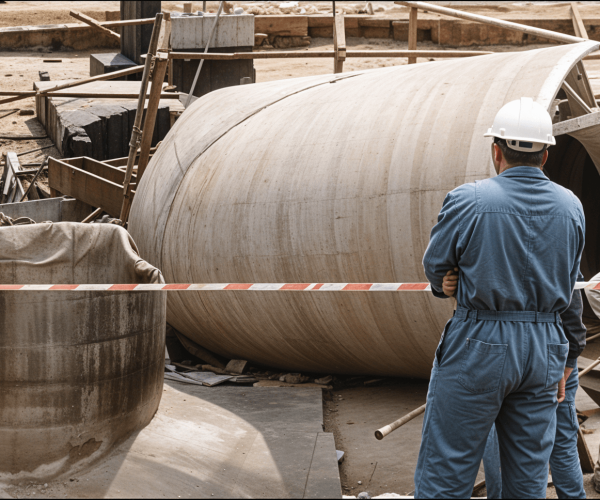
CAPABILITIES
Comprehensive Analysis of Dynamic Failures in Piping Systems
Sudden pressure changes in piping systems can cause water hammer effects, leading to pipe failures, expansion bellow damages, or even catastrophic equipment damage. DRG simulates these scenarios to understand the root cause and offers solutions that involve improved venting strategies, valve closing times, and better piping support arrangements.
Systems subjected to flow-induced vibrations often experience fatigue in welds, nozzles, or attached equipment. Our expertise includes diagnosing the cause of these vibrations—often linked to transient flows, slugging, or flashing—and providing targeted solutions, from structural reinforcements to optimized operational procedures.
Heat exchangers, nozzle connections, and pressure vessels often fail due to rapid thermal expansion or contraction. DRG conducts thermal stress analyses to determine whether the ramp-up or cool-down rates in these systems exceed safe limits, helping clients avoid costly shutdowns and repairs.
Unpredictable slug flows can impose extreme forces on piping and equipment. By analyzing the fluid dynamics, DRG identifies the formation and propagation of slugs, implementing solutions such as flow dampening, control valve adjustments, and realigning piping configurations to minimize risk.
Systems DRG Provides Failure Analysis For
Ensuring Integrity of Critical Piping and Equipment Systems
Piping systems are prone to issues like water hammer, slug flow, and flow induced vibrations. We evaluate both above-ground and buried systems, ensuring structural integrity under dynamic and static loads.
Jetties face specific challenges such as pressure surges during ship offloading. DRG has extensive experience analyzing these environments and offering solutions to prevent system overloading and failure.
Bellows often fail due to unbalanced forces and pressure surges when incorrectly installed. Our simulations of water hammer effects help determine the root cause and suggest modifications to prevent future damage.
Flow dynamics can induce vibrations or surges that lead to wear and tear in compressors and pumps. DRG performs detailed stress analyses to optimize the mechanical setup and advises on the operational flow settings to minimize fatigue.
Sudden flow initiation in firewater systems can lead to damaging water hammer effects. DRG models these transient events to ensure that the piping and the supporting is adequately designed such that it can handle the shock loads.
Fatigue-induced failure of welded joints and nozzles is a common issue in dynamic systems. By performing vibrational and stress analyses, we identify weak points and recommend reinforcements or redesign.
Heat exchangers are often subject to rapid thermal cycling, causing fatigue or mechanical failure. DRG’s failure analysis assesses the material behavior under these thermal stresses and suggests operational changes or design improvements.
APPLICATIONS
Failure Analysis Project Examples
When the piping system at a facility is extended and the construction phase is completed, the system must be filled to test it properly. Filling an empty system can be risky due to the possibility of trapping large air pockets. The presence of both liquid and gas can result in high unbalanced forces, a good example of shock loading. These unbalanced forces arise because the substances have different momentum when passing through components such as elbows.
This issue can also occur when the piping system includes bellows. Bellows provide flexibility between two pipe segments by decoupling them while keeping them connected. A client requested a failure analysis after a bellow failed during the water-filling process.
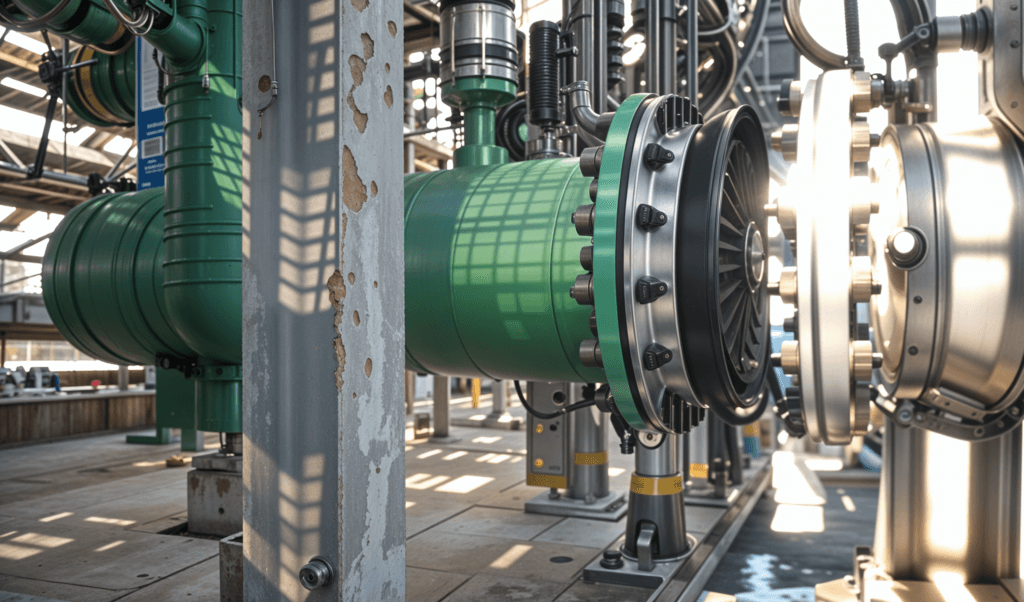
To identify the cause, a surge analysis was first conducted to determine the surge loads triggered by the pump start-up. The analysis was performed using the in-house developed software BOSfluids. After that, a detailed stress analysis was carried out with Caesar II to evaluate the support arrangement near the expansion joint.
The analysis concluded that the bellow failure and support yielding were caused by the combination of large surge loads and pressure thrust due to the lack of tie rods. As a result, it was recommended to equip the bellow with tie rods, reinforce the tee directly after the bellow, and modify the tee support, extending it to act as a fixed point rather than just a guide.
One of our clients was involved in the detailed design phase of a piping system for an offshore platform. The piping had to be designed according to the ASME B31.3 Ch. IX Code (2018 Edition). During the process, several non-conformities related to vibration-induced fatigue (VIF) were identified, requiring comprehensive assessment and qualification through advanced computational fluid dynamics (CFD) investigations. This case shows how challenges from various disciplines can intersect.
The study conducted served as a screening for potential failure risks due to VIF. In this case, two types of VIF were distinguished: flow-induced vibrations (FIV), which occur in all piping systems with active flow and are caused by turbulence in the flow regime, and periodic flow-induced excitations (PFIE), which result from vortices originating from the presence of dead leg branches.
First, a steady-state analysis of the relevant piping segments was performed. The lowest vibrational frequency was extracted and compared to the natural frequency. If the ratio exceeded 1, the piping segment was considered critical, requiring a more detailed transient analysis.
The transient CFD analysis integrated dynamic pressures from the pipe walls into vibrational forces. A Fourier transform was applied, revealing that the vibrations excited several frequency modes, leading to resonance. To quantify these effects, a dynamic time history analysis was performed using Caesar II. It was concluded that the stress range within which the pipe vibrated was negligible, rendering the system robust against potential fatigue.